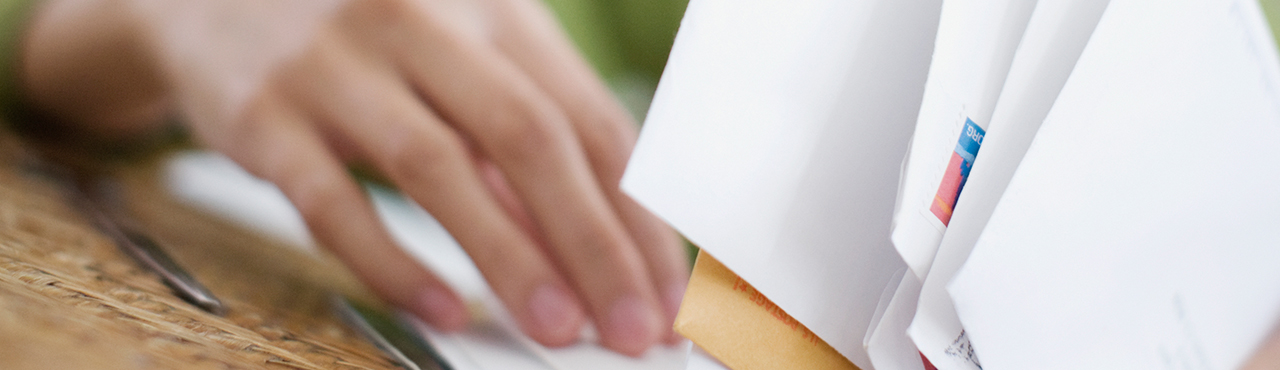
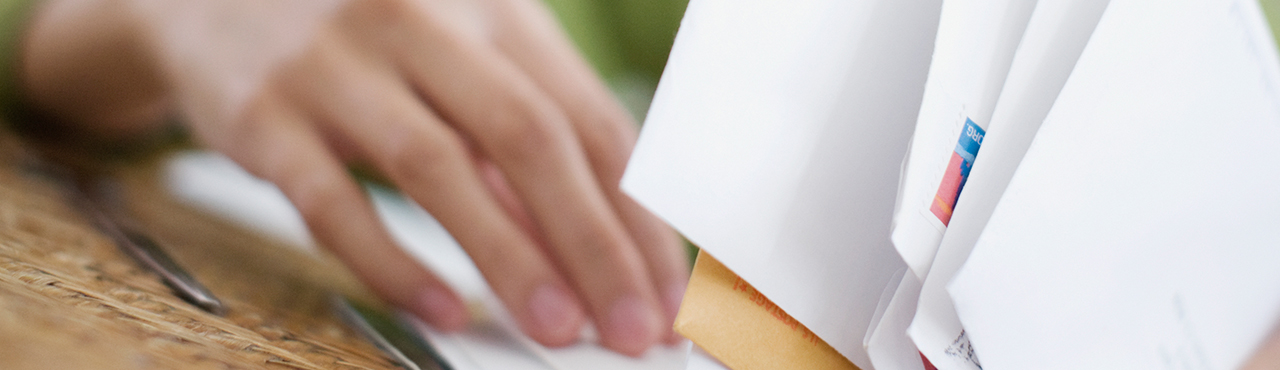
Mail & Ship
The cost of inaccuracy: How mail inserting systems address operational inefficiencies
To ensure contractual SLAs are being met and exceeded, the speed of processing is an important factor for businesses that send a high volume of transactional and bulk marketing mail every day. Consider this: What good is a fast mail centre if it isn’t also accurate? Each envelope your business sends needs to reach its intended recipient, and if the person at the end of the line receives the wrong mail, you could face customer, compliance and operational risks.
For example, what would happen if an existing customer were to receive an upsell offer with someone else’s name on it? You could chalk that up as both a lost business opportunity and a potentially damaged relationship. No prospect would likely give a second thought to an inaccurately addressed mailer, and no customer appreciates feeling like “just another number.” Worse still, if a private financial or healthcare statement were to find its way to the wrong recipient, your business could be violating a number of privacy and security regulations and incurring heavy penalties.
An often overlooked consequence of inaccurate mail processing is the cost to reconcile those mail pieces, according to Lynda L. Hansen, segment marketing manager at Pitney Bowes.
“When mailing errors occur, it takes time, material and manpower to reconcile and reprocess those mail pieces,” explained Hansen. “That impacts overall operational efficiency and performance, which means money out of your pocket.”
This risk is even present in mail centres that use high-speed inserting solutions. That’s because certain high-speed systems lack robust tracking and precision material handling, which actually exacerbates the issue of detecting a breach.
“We know many situations where systems may process at a great speed, but in the end the actual yield, or pieces processed accurately, is far less than the cost of labour and material,” Hansen explained. “Plus, the time to reprocess is significant.”
Ultimately, businesses need to strike the right balance between speed and accuracy in order to optimise productivity and operational excellence. Automated inserting systems from Pitney Bowes can provide both, offering three major benefits to your mail operations:
01. Smarter complex mail processing
Consider all the different types of mail your organisation sends to customers. From account statements with highly sensitive data to invoices to promotional material, content varies in volume, dimensions, intention and destination. How do you ensure all the mail was processed accurately while maintaining maximum profitability and cost efficiency?
Having the right finishing solution for the job can make all the difference. For example, a high-integrity inserting solution from Pitney Bowes is able to process mail at variable rates of speed – anywhere from 10,000 to 26,000 cycles per hour – to maximize the highest level of productivity for the job.
While other systems might have to slow down processing to ensure accuracy, Pitney Bowes solutions maintain integrity without compromising high productivity. Precision tracking and advanced material handling capabilities enables you to process highly complex jobs, including those with multiple streams and multiple match requirements, at speed. Selective insertion and matching ensures that secure transaction mail is not mixed up with general direct mail, while also accounting for factors such as variable page counts and adjusting for corrections instantly to reduce mistakes.
02. Improved processing efficiencies
Stepping up from older to modern inserting systems makes a big difference as it enables new levels of productivity and operational excellence.
Automated configuration ensures consistent, repeatable results, removes the risk of human errors during setup, and simplifies changeover to reduce downtime. Newer systems also incorporate precision material handling with dynamic skew detection to maintain system uptime and reduce jams, outsorts and other negative outcomes. And by measuring yield per labour hour, modern inserting systems ensure you are tracking accuracy against production cost per piece.
With an efficient inserting system, you’re able to meet faster, higher output while maintaining – or even decreasing – the cost of production. Pitney Bowes inserting solutions are able to deliver 20 percent increased efficiency over traditional systems. That means you can better manage personnel on the floor and re-allocate work resources toward other tasks.
Modular inserting systems offer the benefits of the latest processing technologies while helping you manage the cost of investment. Rather than overhauling your entire mail centre, you can upgrade quickly, easily and in a way that’s less restrictive to your bottom line.
03. Attractive customer communications
With the right inserting system, you can enhance the quality and appeal of your customer communications. For example, take advantage of compelling direct mail campaigns that incorporate personalised messaging and full colour messaging on the outside of each envelope. That’s a great way to increase customer engagement on targeted cross-sell campaigns.
These benefits are possible without sacrificing operational efficiency and accuracy. Pitney Bowes solutions allow you to make each piece of mail personalised and relevant at a level of quality, accuracy and productivity you can’t achieve with other systems.
For an efficient mail finishing solution that can also deliver accuracy, speed and improved mail centre productivity, review our high-speed mail inserters to find the solution that’s ideal for your organisation.